Working Process
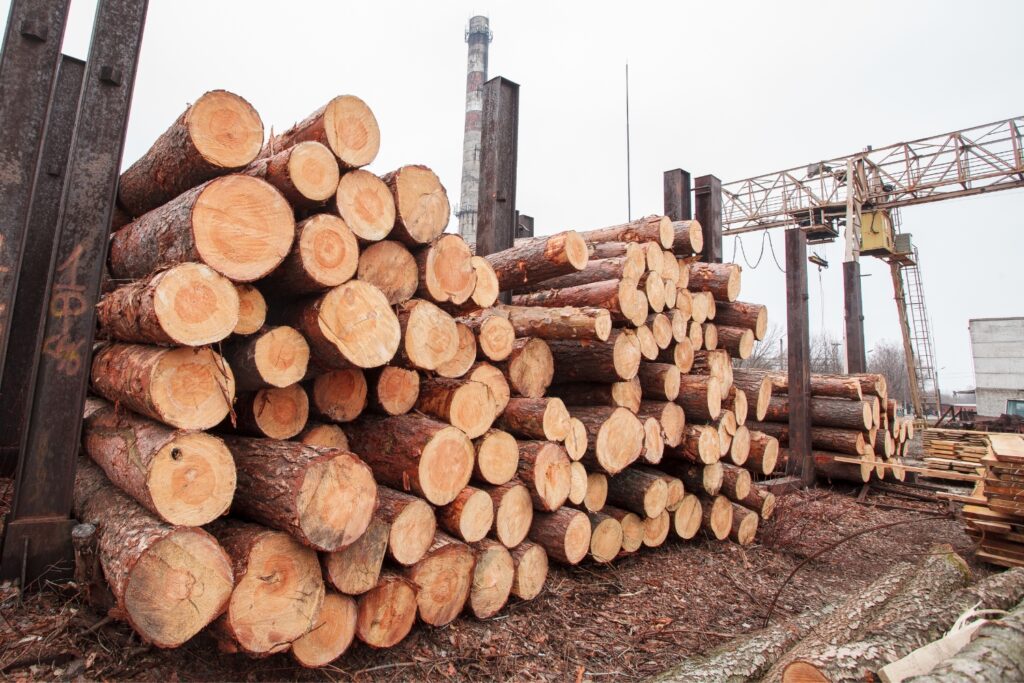
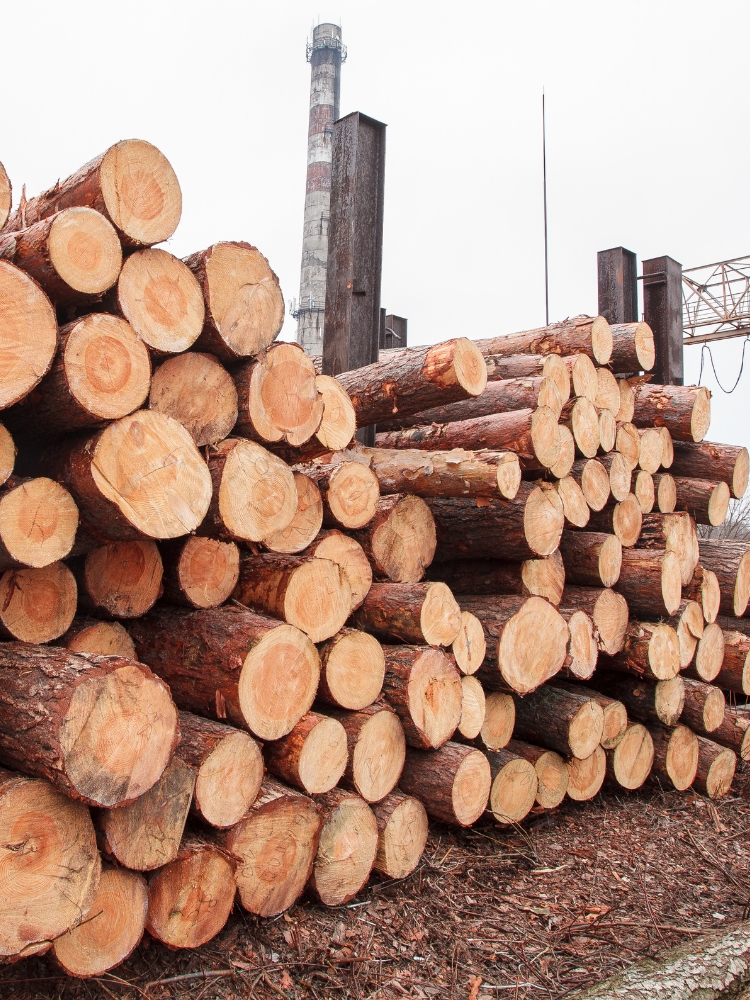
Step 1: Wood Selection
The first crucial step in the furniture manufacturing process is carefully choosing the appropriate material. The selection of wood should be based on the specific piece of furniture you intend to produce. For example, when manufacturing heavy furniture such as wooden tables and bedframes, it is essential to opt for sturdy and durable materials like hardwoods, including mahogany, teak, and oak.
Hardwoods are capable of withstanding daily use, providing excellent support for weight, and can be easily maintained through waxing and polishing, ensuring their color and smooth finish last for many years. On the other hand, if you are creating decorative items such as kitchen cabinets, supporting beams, window frames, or outdoor decks, softwoods such as fir, ash, or birch are more suitable options.
Step 2: Wood Transformation
The next step in the furniture manufacturing process involves transforming the harvested trees into manageable beams and planks, commonly known as lumber (in North America) or timber (elsewhere). These pieces of lumber serve as the raw material for creating wooden furniture. To ensure the wood’s stability and quality, the lumber undergoes a kiln-drying process. This process allows the wood to reach its equilibrium moisture content (EMC), preventing it from gaining or losing moisture due to its surrounding environment while retaining its essential properties.
The transformation of wood takes place at the sawmill, where skilled professionals carry out the necessary procedures. This comprehensive transformation process typically spans around 2 to 4 weeks to ensure that the wood is properly prepared for its subsequent use in furniture production.
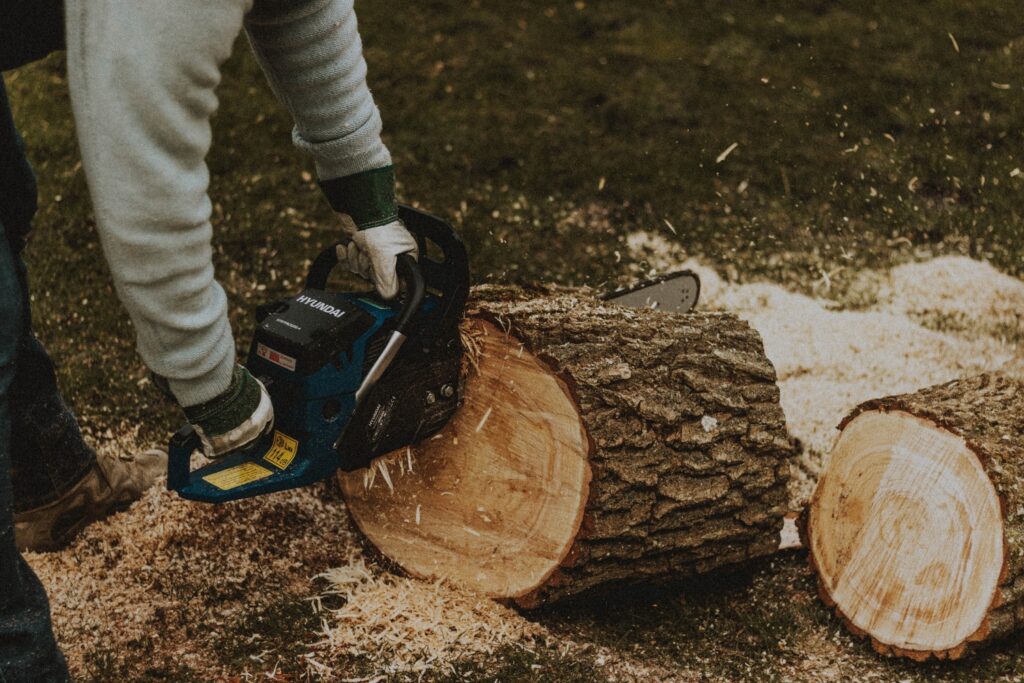
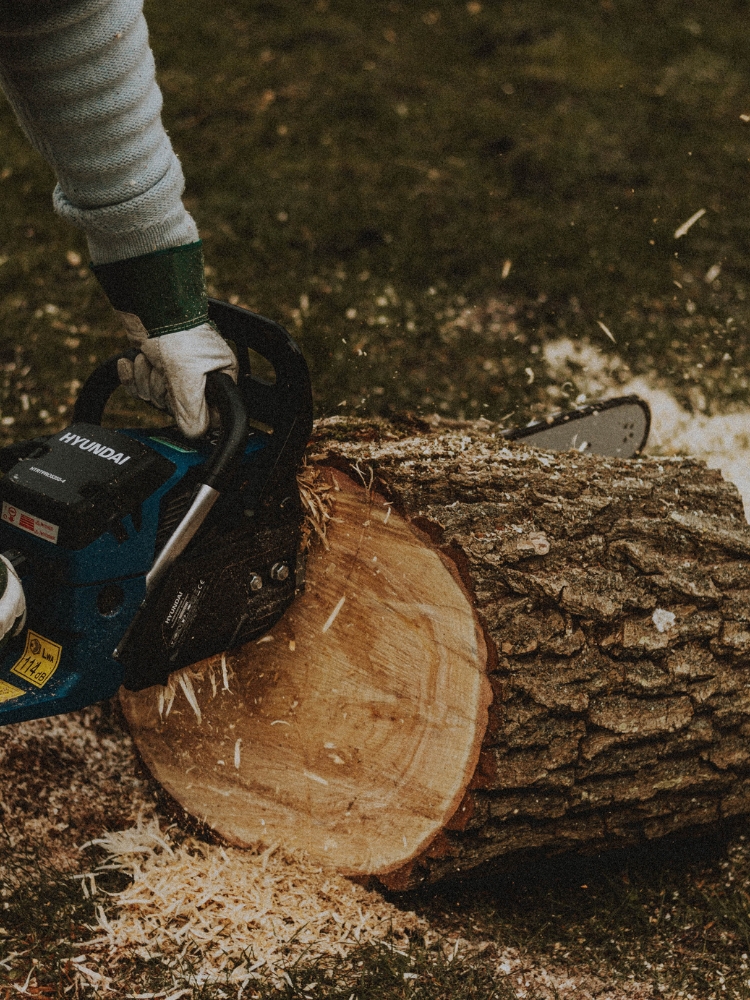
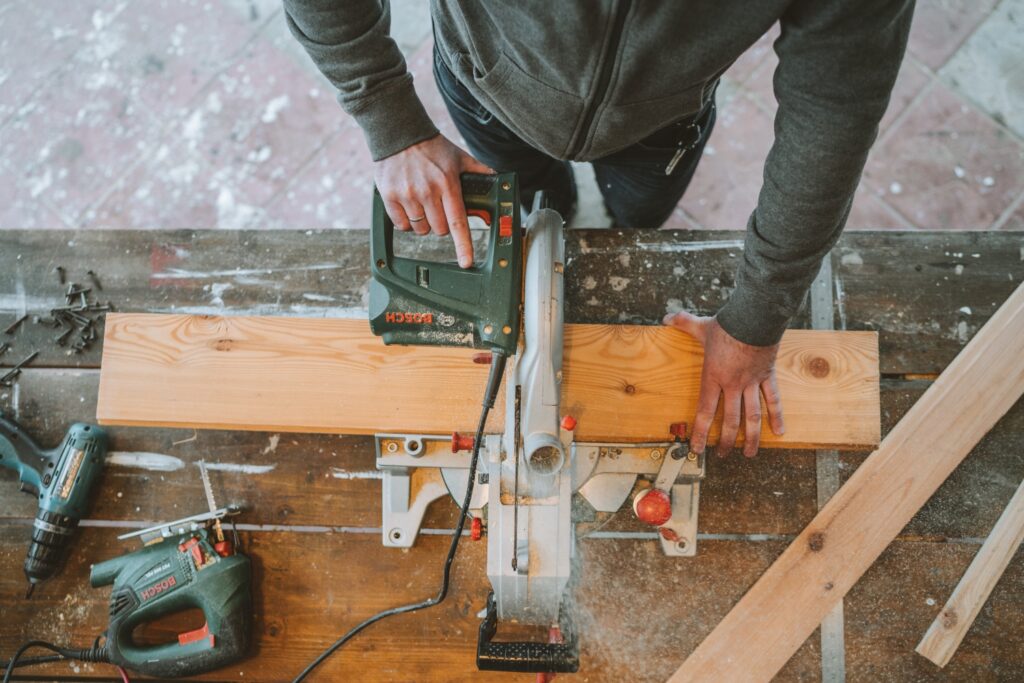
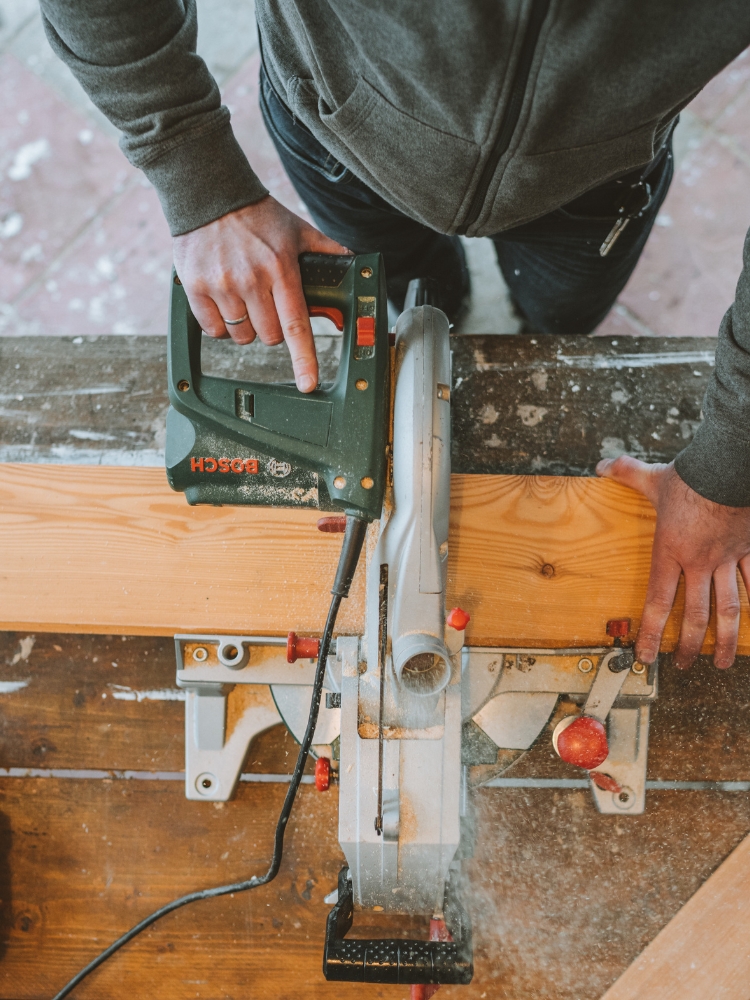
Step 3: Wood Splitting and Finishing
After kiln drying, the wood is shaped and refined in a machine shop through sawing, planing, molding, and grooving. Individual parts are cut, assembled, and secured with clamps. High-speed rotating knives precisely shape each piece. Machine sanding ensures a smooth, uniform surface, followed by hand carving for intricate details. Veneering is performed if needed, enhancing appearance with decorative wood bonded to the surface. Jointing techniques like tenoning, doweling, and dovetailing create strong connections between components, ensuring durability.
Step 4: Assembly and Quality Check
Wooden carcasses are assembled, drawers are glued, and doorframes are put together. After setting the glue and applying clamps, the piece undergoes necessary machining for joint sanding and edge shaping. It is then returned for final structuring, including glue cleaning, hand sanding, and applying finishes like staining and spray polishing. A thorough quality check ensures adherence to craftsmanship and durability standards, making necessary adjustments for a flawless end product.
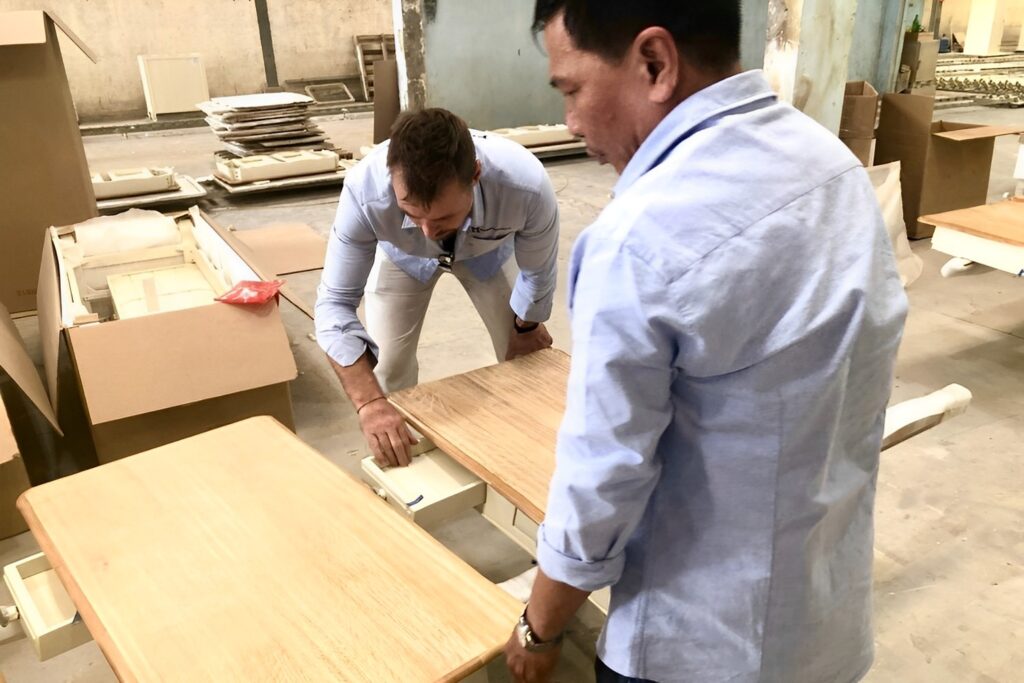
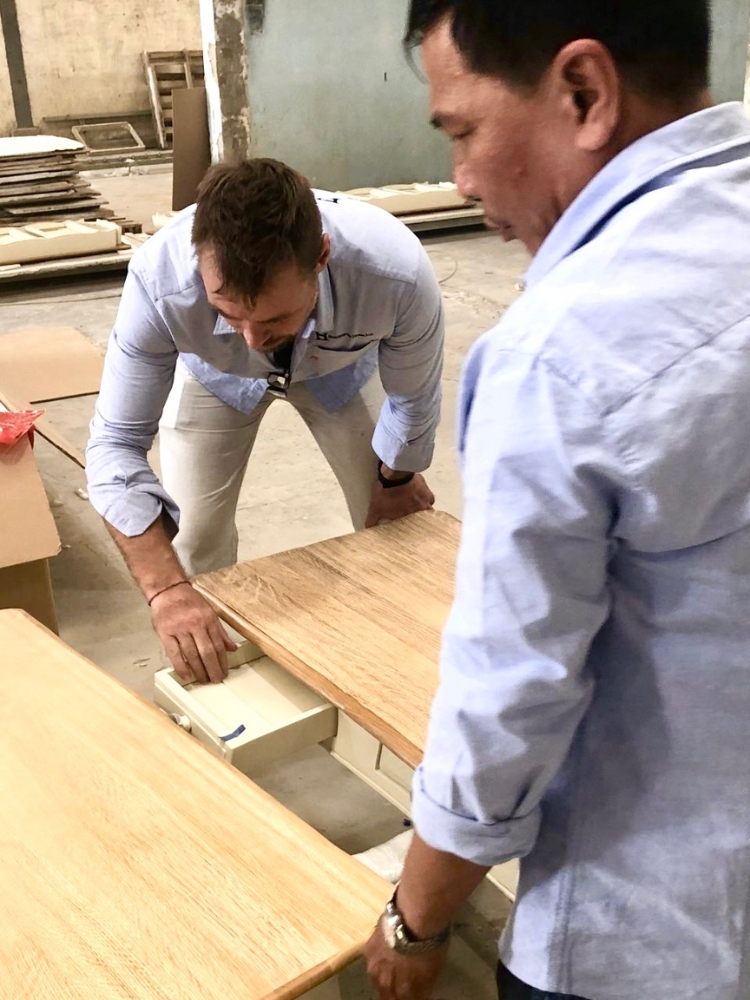
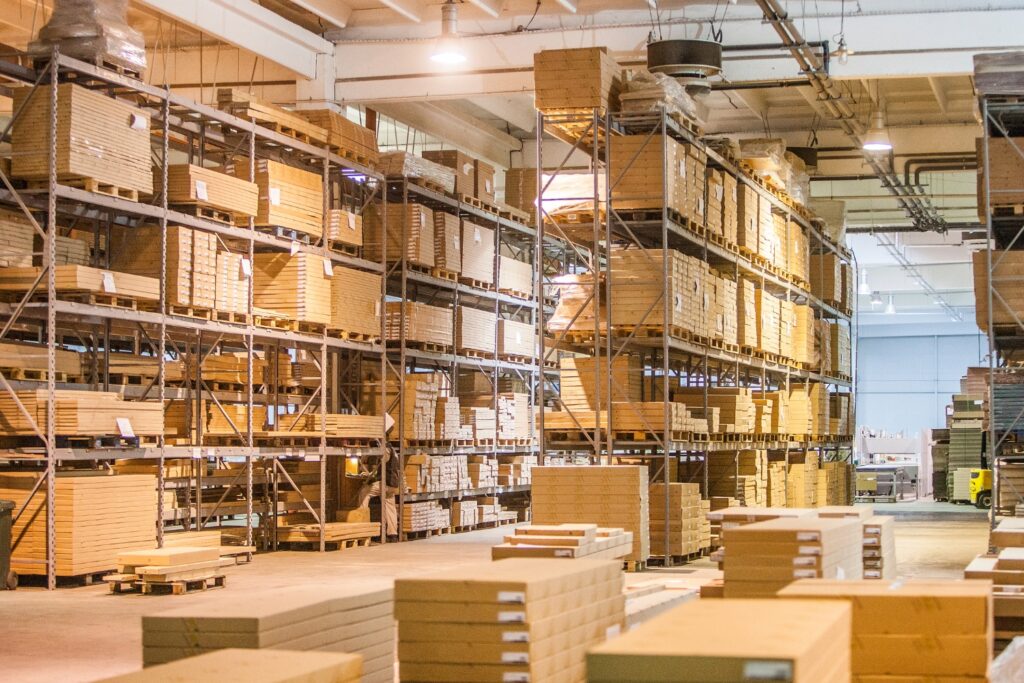
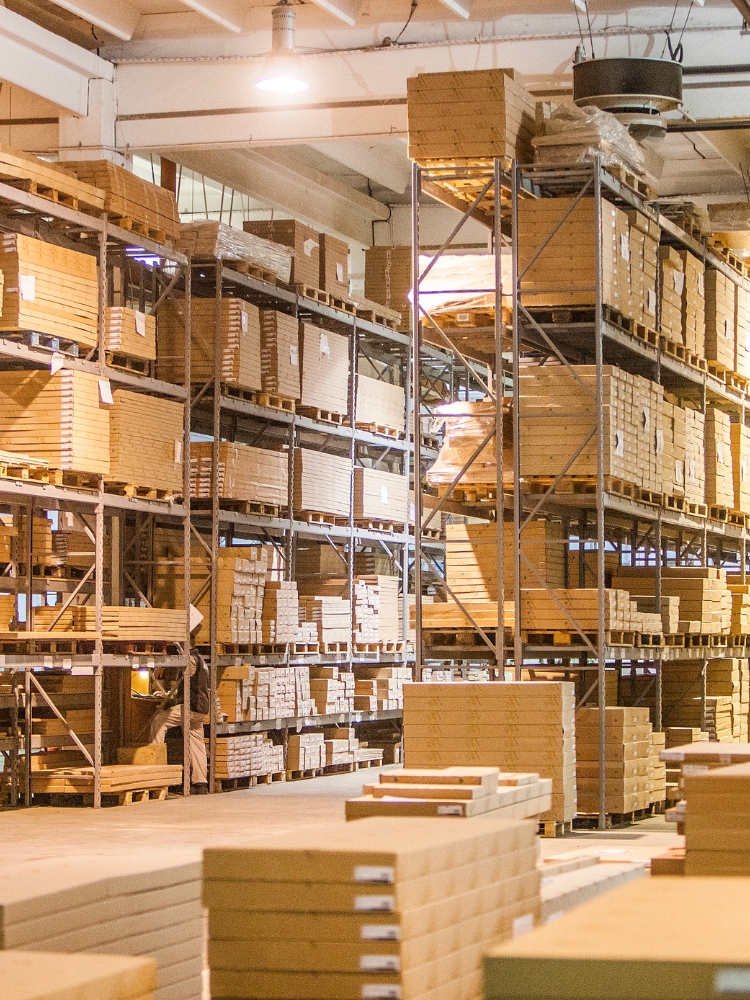
Step 5: Packaging and Container Stuffing
Once approved by our or authorized third-party quality checkers, the products are prepared for export. Our packaging process prioritizes environmental impact and complies with pollution laws in different countries. At Rusteak, we use sustainable materials like recyclable PPE products and recycled cartons for minimal but durable packaging.
We take pride in ensuring our packaging can withstand challenging logistics conditions, guaranteeing that the product arrives in impeccable condition to the end customer. By handling the container stuffing in-house, we minimize transfer points and ensure the goods reach the buyer’s warehouse in perfect condition, reducing the need for additional transfers.